10 best practices to follow in supply chain execution
Best practice is a group of tasks that optimizes the efficiency (cost and risk) or
effectiveness (service level) of the business discipline or process to which it contributes. It must be implementable, replicable, transferable, and adaptable across industries.
Gartner
The business of supply chain management involves many stakeholders including business units, vendors, suppliers, truckers, warehouses to name a few. Successful supply chain management can be achieved through the implementation of best practices in all areas of the chain including, planning, sourcing, production, and distribution. This in turn ensures efficient service delivery and improves profit.
Below are some of the best practices in supply chain that companies can implement to be successful, sustainable, and profitable.
- Talent identification and retention
- Organisational alignment
- Supply chain strategy
- Performance management
- Cost management
- Supplier alliances and management
- Identifying and managing risks
- Effective payment processes
- Sustainable supply chains
- Investment in software
Talent identification and retention
Supply chains have become highly globalised and have evolved to handle the full spectrum of activities from sourcing to production planning to delivery and service. While they are evolving consistently thanks to modern technology, supply chain leaders are finding it difficult to source the right talent for the job.
Only 38% of supply chain managers were confident that they have the right talent to handle supply chains currently.
Deloitte
Hiring specific talent required to handle the requirements of the modern supply chain may require a specialist recruitment company that focuses on supply chains. Many of these specialist supply chain recruitment companies work with universities, colleges, and other professional bodies in supply chain to create a pipeline to ensure a steady flow of students, interns, and entry-level workers to supply the industry requirements.
While hiring in supply chain is a challenge, talent retention is another area where some of the best practices must be followed. Some of these best practices include investment in training for new and existing staff as well as providing a measurable roadmap towards career development.
Organisational alignment
Organisational alignment is key to the successful operation of a company and its supply chain. Organisational alignment happens when all departments understand the goals of the business and work collectively to achieve that goal. Many supply chains have been operating in silos, leading to ineffective communication, gaps in data flow and unreliable process outcomes. Cross-training, and cross-department execution is critical in aligning the company to achieve an efficient supply chain.
Companies need to ensure all supply chain processes are standardised and evaluated on their strengths and weaknesses. It is also imperative that all business units collaborate, coordinate and orchestrate their tasks. Once the processes are implemented, the impact of these changes must be audited regularly to ensure all practices are aligned.
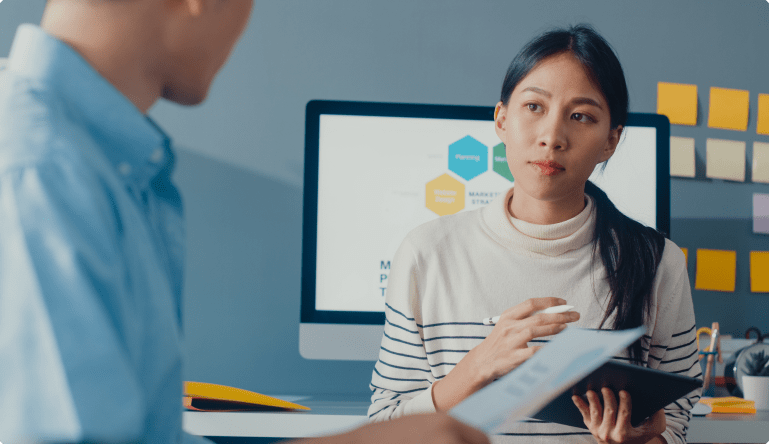
Strategy
Strategy is important in any supply chain operation, and this begins with identifying and defining the needs and opportunities in the operation to create a plan based on the available resources. These resources range from people, processes, and technologies within the company. The mission of the supply chain operation must be aligned at a corporate level, as success can only be met when there is a full adoption of these practices by supply chain leaders.
The strategy should include simplification, refinement and standardization of sourced products and services. Eliminating redundancy, process improvement and tracking cost savings from sourcing is also key.
Performance Management
Once the above strategies are in place, they must be monitored for performance. Supply chains should be flexible, agile and resilient when responding to market changes and local requirements while ensuring changes in costs are consistently monitored. Performance metrics or key performance indicators (KPIs) should be linked to strategic objectives and standard operating procedures relating to the supply chain. KPIs allow companies to identify and analyze the strengths and weaknesses of their supply chains to address inefficiencies based on data-driven insights.
Depending on the type of supply chain operation, these KPIs may include supply chain cycle time, order rate, inventory-to-sales ratio, logistics costs which enable the company to monitor the ratio of error-free orders, available inventory, total cost of ownership (TCO), speed of replenishment and the total cycle time from order placement to delivery.
Cost management
Cost management and TCO incorporates all costs associated with various operations within the supply chain from sourcing, production, storage, distribution, and financial and trade costs. Understanding the impact of inventory carrying costs, returns, logistics and distribution costs, order management costs, special deliveries, and payment cycles (both receivable and payable) will bring clarity and possible cost savings to the operation.
TCO allows supply chain managers to make informed decisions about all supply chain nodes and other departments which form supply chain strategies.
Supplier alliances and supplier management
Supplier alliances and supplier management processes are key to ensuring that strategies and cost reduction initiatives work well. Efficient supply chain management can be achieved only through collaborative partnerships and creating a win-win strategy for the company and the supplier. If the supplier feels they are being consistently forced to drop their prices, they will constantly be on the lookout for better paying competitors and will drop lower paying customers quickly based on the demand.
Supplier management strategies must be based on enhancing business, financial and process objectives. Performance incentives, a focus on improving price matching and achieving price accuracy and prompt payment schedule is also vital in this process.
-min.png)
Risk Management
Supply chain leaders must understand that while long-standing supply relationships can create value, disruption of such relationships can have devastating impacts and need to be managed effectively. Companies must do a risk assessment at the beginning of every major supply chain project. A formal risk management process must be documented and implemented to identify, prioritize, and mitigate supply chain risks looking at the future.
This process must cover various events that could be catastrophic to supplier relationships and the supply chain. Trade wars, tariff adjustments, weather patterns or shipping disruption like the one we are facing currently all can have a negative impact on supplier relationships.
Known and identifiable risks in distribution, fluctuation in demand, non-compliance of regulatory processes all can be identified, measured, managed, quantified in order to take proactive action to mitigate such risks.
Sustainable supply chains
Sustainable supply chains have become a necessity as customers become increasingly conscious about CO2 footprints and the environment. Extensive research done by NYU Stern’s Center for Sustainable U.S. consumers’ purchases consumer packaged goods (CPG) found that 50% of CPG growth from 2013 to 2018 came from sustainability-marketed products indicating that customers are migrating more towards sustainable products. Digital supply chain platforms can assist companies in reducing their carbon footprint.
Consumers are voting with their dollars against unsustainable brands. The legacy companies that will thrive are those that accept this shift and are willing to pivot
Harvard Business Review
Payment processes
Supply chain relationships could also fail due to a lack of best practices and discipline in payment processes both upstream and downstream. The order-to-pay process or procure-to-pay process needs to be automated as it covers all steps of the supply chain from order placement to final payment. This covers various departments, including finance, sales, warehousing, and logistics, all of which could be working in silos using various systems to run their operations.
A unified digital supply chain platform can simplify the entire process, from supplier management, order placement, delivery, and final payment. This ultimately improves visibility across the entire supply chain, providing key insights into payment processes and efficiency.
Digitalizing supply chains
Many companies still manage their supply chain operations using archaic technologies like spreadsheets and ERP extensions which do not provide the required solutions. Different parts of the supply chain often use different standalone systems and manual processes which could create costly errors in a fast-moving business environment.
A successful and efficient supply chain must have access to real-time information and detailed supply chain analytics to ensure that supply chain managers are able to formulate data-driven strategies and take data-driven decisions where required. Digital supply chain platforms provide comprehensive supply chain management solutions that integrate automation and predictive analytics, capable of handling all aspects of the supply chain.
Key take-away
Supply chain and its management have become vital for many companies success, and its importance is being seen as a competitive advantage and differentiator throughout companies. The best practices described herein provide a solid starting point for supply chain managers looking to enhance customer satisfaction through effective supply chain management.
The use of technology is vital in turning these best practices into reality, setting the company on a path of successful supply chain management and achieving high customer satisfaction; enabling long-term success and growth.
Supply chain managers are constantly looking to find new and innovative ways to manage supply chains and find opportunities for improvement and solving issues. Digital supply chain platforms can bring data and functionality together giving supply chain managers a real-time view of the current state of their supply chain, predicting any future problems leading to enhanced collaboration, planning and execution.