How to overcome challenges of last-mile logistics
Last-Mile or Last-Mile delivery refers to the final step in a shipment’s journey. The last-mile is the processing of a product from the destination terminal or port to the consumer’s door. This final step takes place after the Mid-Mile process; wherein a product is dispatched from the manufacturer’s warehouse and is then handed over to a carrier responsible for transporting it to the destination by mode of sea, air, rail, or road. The Last-Mile is essentially the most crucial part of the process, as its execution acts as the driving force in customer satisfaction and overall company performance.
Challenges currently facing last-mile operations
A successful Last-Mile delivery faces several challenges and if not handled properly, can have a substantial impact on customer satisfaction. From big enterprises to small-scale shippers, successful execution of last-mile operations is critical to their business as it affects overall customer experience and business performance. The challenges outlined below are common among a range of service providers. Those most affected are companies with high costs and complexities in operations related to the size of the movement and congestion. This ultimately impacts the On Time In Full delivery. Some of the major challenges that impact last-mile logistics are:
Congestion: The majority of cargo flow from the Mid-Mile ends up at a terminal, depot, or warehouse; all of which have issues currently with congestion. Congestion refers to the delay in pick-up of cargo which impacts the delivery.
Capacity: The lack of trucking capacity caused by increased demand or congestion is preventing the quick turnaround of trucks. This is prevalent in places like the US, where increased container and cargo dwell times occur as a result of chassis turnaround.
Transloading: Shortages in warehouse space, primarily close to gateways, are causing the movement of cargoes further out. This in turn involves the transloading of goods at additional costs before the delivery is affected.
The last-mile is one of the complex elements to organize in the supply chain as it reconciles various stakeholders (both customers and service providers) with a mix of shipments and the above-mentioned challenges. Such complexities create frustration for companies and can result in delayed delivery to clients and unsatisfied customers.
Apart from congestion, capacity, and transloading, there is a slew of additional constraints facing Last-Mile operators.
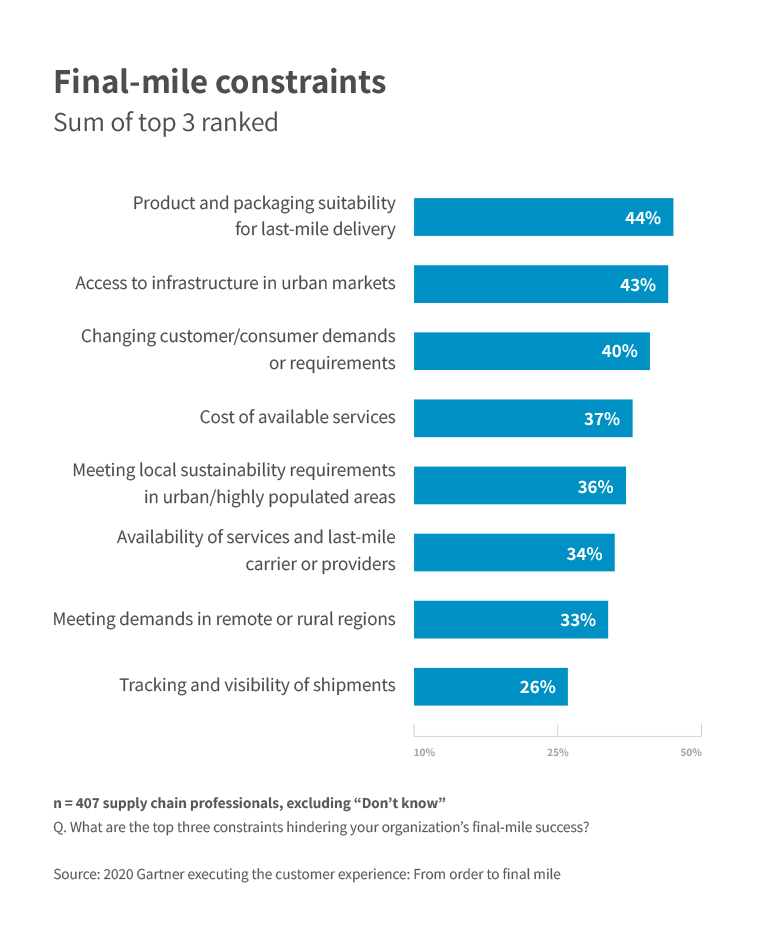
Solutions for last-mile challenges
Optimising the Last-Mile and providing the most cost-effective consumer experience is critical in supply chain. There are a few solutions that can help deal with Last-Mile challenges and enhance the processes internally.
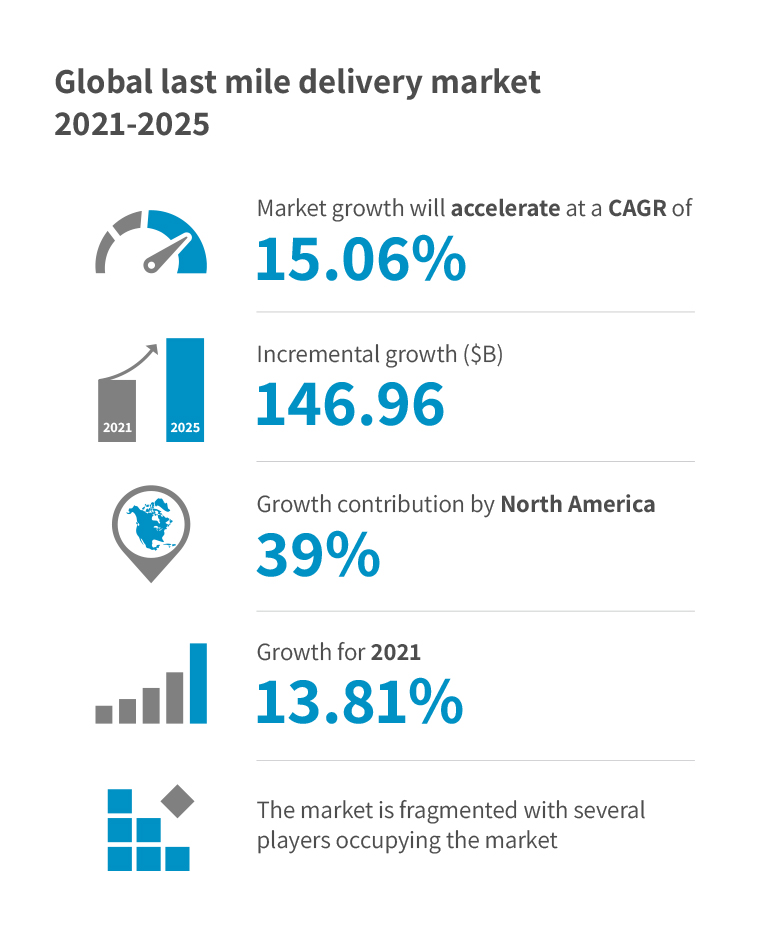
Technology and digitalisation are rapidly becoming the heroes set to save Last-Mile delivery challenges. There are several digital solutions available to address these complexities such as;
Digital visibility and SaaS platforms are slowly gaining momentum in the market as many companies are adopting them. These platforms have many advantages; such as easy implementation and reasonable set-up costs. In addition, the scalability of these cloud-based platforms widely suit customer requirements.
Electronic Logging Devices or ELDs help execute efficient service in the Last-Mile by targeting aspects such as trip inspections, directions, pod capture, and exception reports. ELDs also curate load, route, customer, and asset data which are all readily available in real-time to those who have access to the system.
Fleet Management Systems or FMS can be used for record-keeping and receiving updates on proof of delivery, percentage of on-time in-full delivery, exceptions and other KPIs set as part of the last-mile delivery strategy. These KPIs provide insights to the Last-Mile operator about the operating efficiency of the vehicle and the customer experience. FMS can be integrated into supply chain visibility platforms, allowing customers and companies to access the information through the system dashboards.
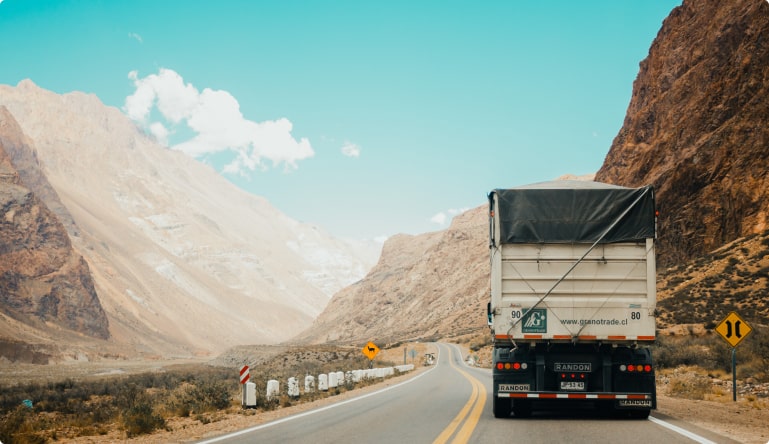
Routing/Scheduling systems can set the most optimised route for the vehicle reducing miles traveled by leveraging distributed and centralized routing for the vehicles. This tool is readily integrated with many enterprise resource planning systems, TMS, or as part of supply chain digital platforms.
Improving visibility, especially in the Last-Mile, is an important prerequisite for ensuring customer satisfaction and loyalty as a growing number of customers are demanding real-time information on their package’s location.
One of the ways this can be achieved is to adopt a mobile-first strategy. A mobile-first strategy enables customers to use their smartphones, tablets and tracking apps as tools for achieving visibility is critical in Last-Mile operation.
Last-mile delivery was identified as the most inefficient process of the entire supply
chain, by 59% of transport and logistics companies in the U.S. and 78% in Canada, 74% in the U.S. and 80% in Canada agree that their organization would benefit, or have already benefited, from an effective mobile-first strategy for last-mile delivery. 49% of respondents in North America with mobile-first strategy in place for Last-Mile delivery said that it has effectively reduced their operational costs.
- A global report "The Last Mile Sprint: State of Mobility in Transportation and Logistics" found
Reducing high delivery costs is key as Last-mile delivery is an expensive leg in the supply chain for both companies and customers. By leveraging the available technologies that support timely deliveries, these costs can be reduced. Companies must also account for a budget for instances of failed deliveries, rerouting, compromised timelines, customer unavailability and other exigencies.
Using the latest technology is a driving factor in remedying the aforementioned challenges. Nearly half of global transportation and logistics companies use outdated technology for Last-Mile delivery. By using the latest advanced technologies, which can monitor the last-mile movement, predict potential hurdles, and devise proactive strategies to deal with them, companies can reduce delays and high delivery costs.
Key take-aways
Last-Mile delivery is the final frontier in supply chain execution, and the most crucial one, as this is where the customer experiences a company’s performance. This experience will be the driving force in deciding whether they use a company’s services or not.
Modern technologies such as AI, drones, and machine learning are ultimately the components needed to propel successful Last-Mile initiatives into the future. Supply chain managers must consider the costs of procuring these technologies as an investment rather than as an expense as these technologies not only optimises the Last-Mile operation but in turn aid in the reduction of resources and time
Communication, transparency, and collaboration are critical in achieving customer satisfaction in supply chain. Digital platforms have the capability to send alerts and notifications throughout the delivery period to customers right from despatch to transit to delivery.